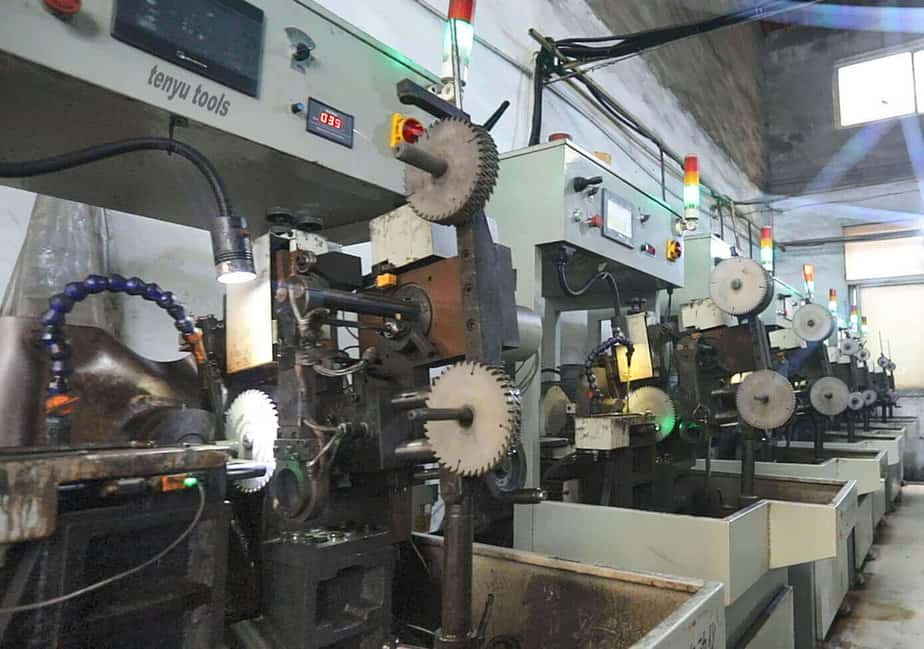
How to Select the Correct Saw Blade Manufacturer?
How to Choose the Right Saw Blade Manufacturer?
Finding a saw blade manufacturer you can trust is like finding a good mechanic—once you’ve got one, you hold onto them. Here’s what I’ve learned about making that choice.
Select a manufacturer who offers high-quality products, customization options, strict quality control, efficient delivery, and responsive customer support. These factors ensure you get blades that meet your needs and help your business succeed.
Building a Partnership with Your Manufacturer
Over the years, I’ve realized that the manufacturer you choose becomes a partner in your success.
· Quality: High-quality blades perform better and last longer, which is something my clients appreciate.
· Customization: Being able to have my logo on the blades or request specific features sets my business apart.
· Quality Control: Manufacturers with certifications and strict QC measures are more reliable.
· Delivery Efficiency: Efficient logistics help keep projects on track.
· Customer Support: Responsive support is invaluable when issues arise.
It’s worth taking the time to research and even reach out to potential manufacturers to see how well they align with your needs.
Conclusão
At the end of the day, selecting the right saw blade and manufacturer boils down to understanding your needs and doing a bit of homework. It’s an investment of time that pays off in quality results and smoother operations.
What are the Different Types of Saw Blades?
Have you ever stood in front of a wall of saw blades, feeling a tad overwhelmed? Trust me, you’re not alone. Let’s break down the different types to make things easier.
Saw blades come in various types like rip blades, crosscut blades, combination blades, and specialty blades such as dado and abrasive blades. Each one is designed for specific cuts and materials, so knowing the differences helps you pick the right blade for the job.
Understanding Saw Blade Types
I remember when I first learned about saw blades—it was like discovering a whole new language.
· Rip Blades: Great for cutting along the wood grain; they have fewer teeth but make quick, rough cuts.
· Lâminas de corte transversal: With more teeth, these give you smoother cuts across the grain.
· Lâminas Combinadas: The jack-of-all-trades, handling both ripping and crosscutting if you don’t want to switch blades constantly.
· Specialty Blades: For instance, dado blades are perfect for cutting grooves, which I found invaluable when working on a bookshelf project.
The key is to match the blade to your material and the cut you need. It saves time and gives you better results. Plus, understanding these types helps when you’re discussing options with a manufacturer—they’ll appreciate that you know your stuff.
What Saw Blade Makes the Smoothest Cut?
If you’ve ever run your hand over a freshly cut piece of wood and felt that silky smoothness, you know how satisfying it is. So, what blade gives you that perfect finish?
Blades with a high tooth count and an alternate top bevel (ATB) grind provide the smoothest cuts. Using a fine finish blade with 60 to 80 teeth ensures clean, precise cuts with minimal sanding required.
Achieving That Perfect Finish
I recall working on a custom dining table for a client who was a stickler for details. Using an 80-tooth ATB blade made all the difference. The cuts were so smooth that I barely needed to sand before finishing.
The secret lies in the blade’s design:
· High Tooth Count: More teeth mean each tooth takes a smaller bite, reducing tear-out and leaving a cleaner edge.
· ATB Grind: Slices through the wood fibers rather than tearing them.
· Thin Kerf Blades: Reduce waste and require less power, which is great if you’re using a less powerful saw.
Don’t forget about maintenance. A dull blade won’t give you smooth cuts, no matter how many teeth it has. I make it a habit to clean and check my blades regularly—it pays off in the long run.
Why Does My Saw Blade Burn Wood?
Nothing’s more frustrating than seeing burn marks on your workpiece after a cut. I’ve been there, and it’s a real mood dampener. Let’s figure out why it happens.
Burning occurs due to dull blades, slow feed rates, misalignment, or using the wrong blade type. Keeping your blade sharp, feeding material at the right speed, and ensuring proper alignment can help prevent burn marks.
Avoiding the Burn
I once had a project where every cut seemed to leave scorch marks. After some head-scratching, I realized my blade was overdue for sharpening. Dull blades create more friction, generating heat that burns the wood.
Here are some tips:
· Sharp Blades: Regularly sharpen or replace your blades.
· Proper Feed Rate: Maintain a steady pace—not too slow, not too fast.
· Alignment: Ensure your saw’s fence and blade are perfectly aligned.
· Correct Blade Type: Use the appropriate blade for the material and cut.
Choosing the right blade matters. Using a blade meant for ripping when you’re crosscutting hardwood can cause unnecessary friction. Matching the blade to the task is a simple fix that saves headaches.
Call to Action:
If you’re in the market for top-notch saw blades or just want to chat about your options, feel free to reach out to us, I’m here to help you find the perfect fit for your projects.
We’re Revolutionary Produtos
What Sets Us Apart
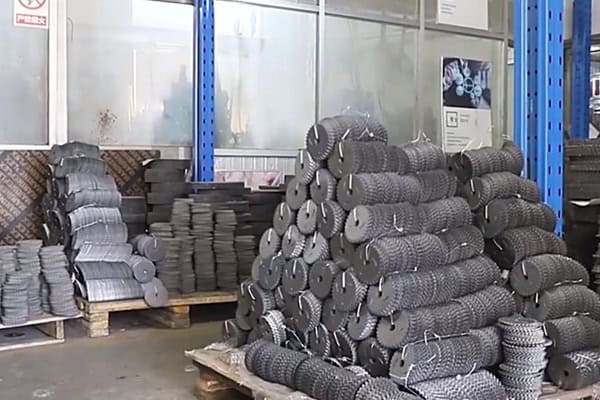
High-Quality Material Selection
Premium-grade materials for durability and optimal cutting performance in various applications.
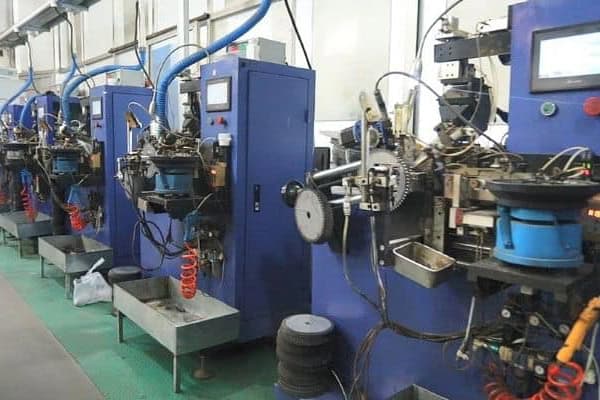
Precision Manufacturing
Advanced machinery and skilled craftsmanship to ensure consistent, precise cuts.
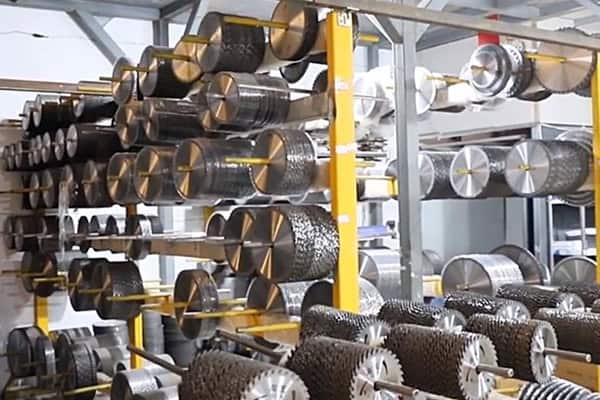
Efficient Order Processing
Streamlined processes to minimize lead times and keep your business on schedule.
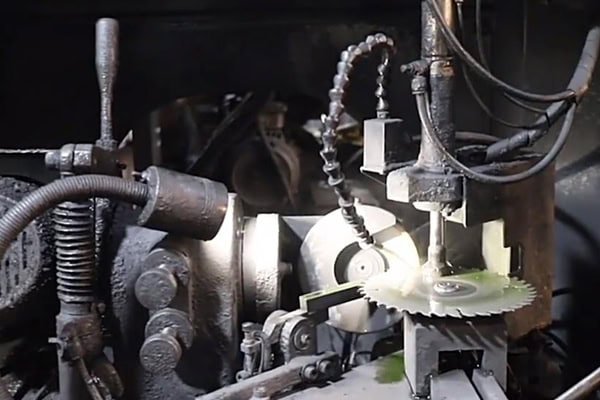
Flexible Order Quantities
Capability to handle both small and large volume orders, adapting to your business scale.
Saw Blade Manufacturer in China
Quality & Precision Your Trusted Manufacturer
Get High Performance Lâmina de serra solutions to Boost Your Sales by 300%.
Strict Quality Control
A dedicated quality control team inspects each blade at multiple stages of production. All products meet international standards and are customizable to fit client specifications, including branding options
On-Time Delivery
Efficient production processes and reliable logistics partners ensure fast and timely deliveries, helping you maintain your inventory schedules without delays.
Professional After-Sales Support
A responsive after-sales service team is available to provide ongoing support, addressing any concerns and offering technical consultations to maximize the performance of the products.
We're There Every Step of The Way
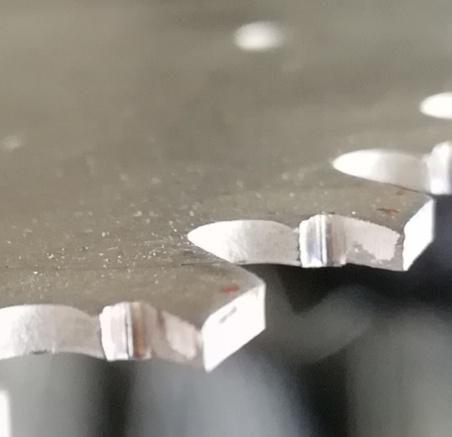
Saw Blade Manufacturer
Premium OKE Tips for Superior Cutting
Saw blades are crafted with high-quality OKE tips for enhanced durability and cutting precision.
Saw Blade Manufacturer
Automated Tooth-Welding Equipment
Full automation in tooth welding ensures accuracy and consistency across every blade.
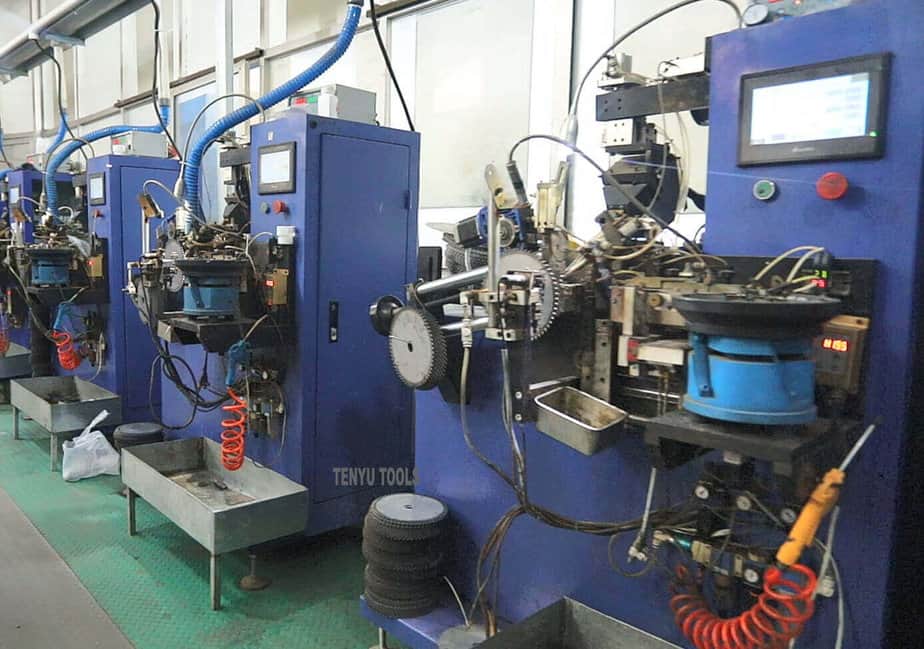
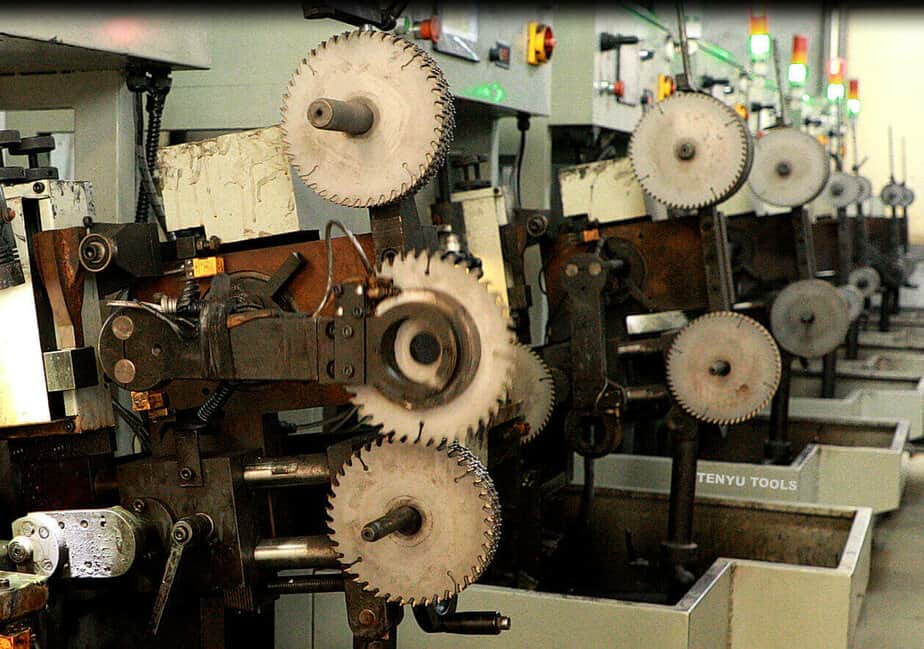
Saw Blade Manufacturer
Advanced Tooth-Grinding Technology
Fully automated tooth-grinding equipment sharpens blades to exact specifications for smooth, efficient cuts.
Saw Blade Manufacturer
Dynamic Balance Testing for Stability
Each saw blade undergoes dynamic balance testing to ensure stability and reduce vibration during use.
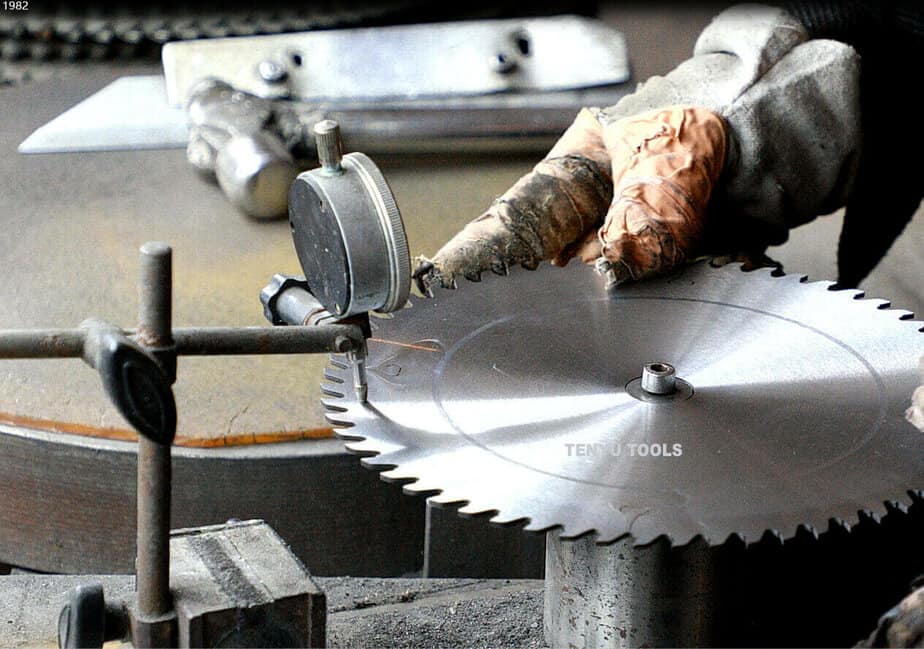
Quality Inspection Apllications
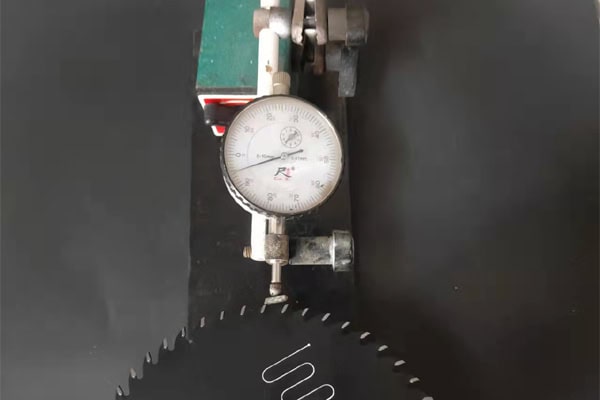
Diameter Deviation Runout
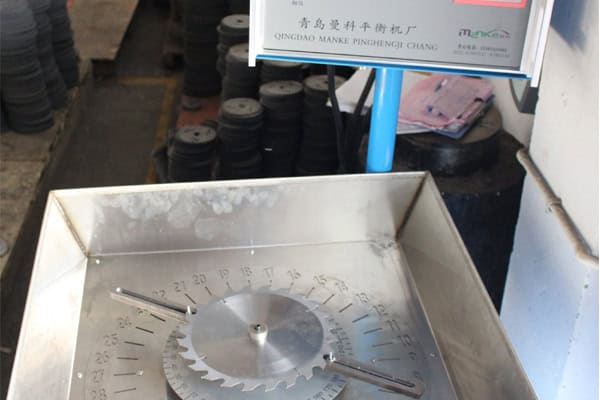
Dynamic Balance Tester
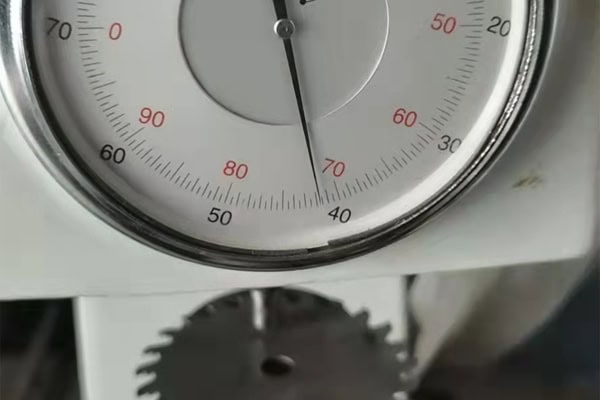
Hardness Machine
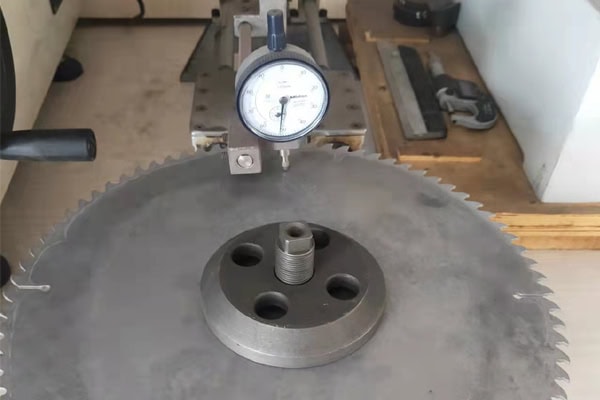
Saw blade Plane Deviation
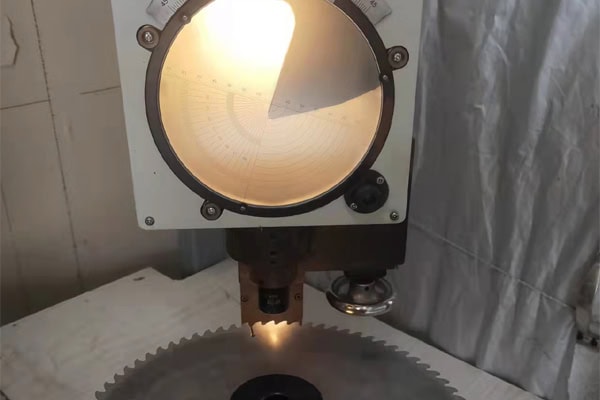
Teeth Angle Check Projector
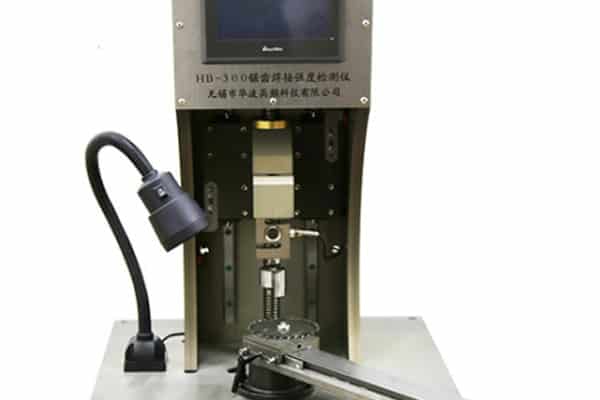
Welding Firmness Tester
Our Factory Insight
From material selection to final inspection, ensuring precision at every step.
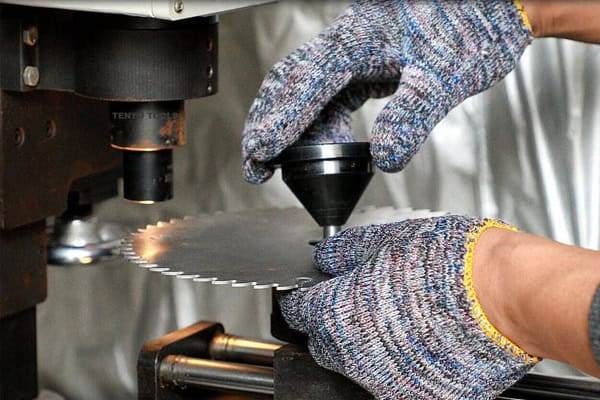
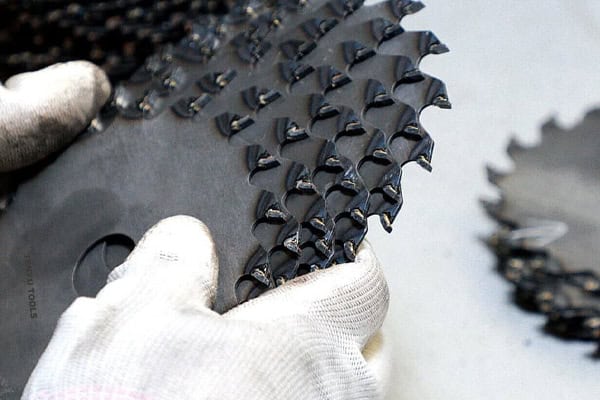
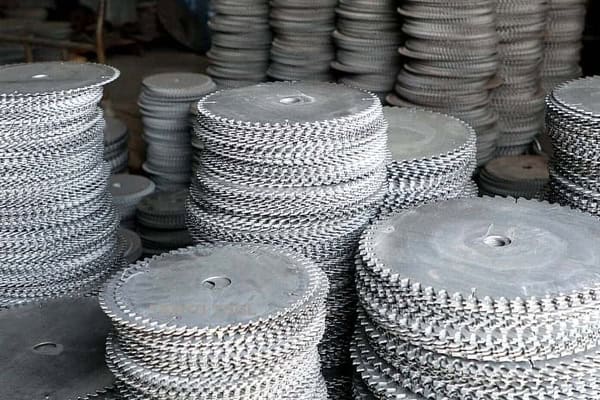
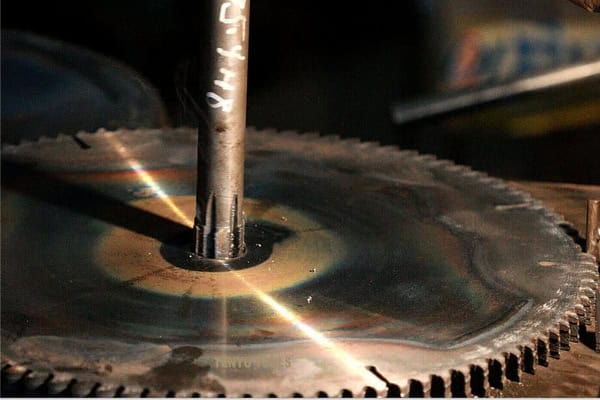
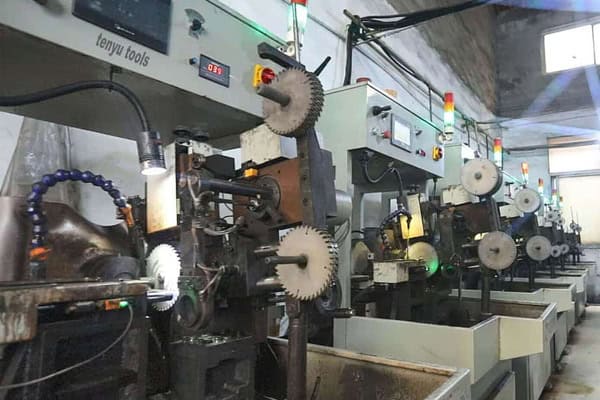
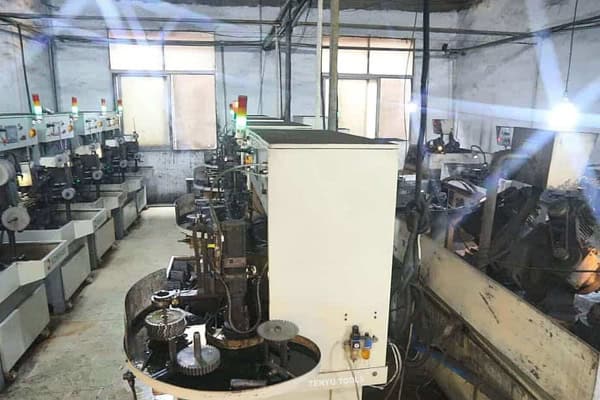
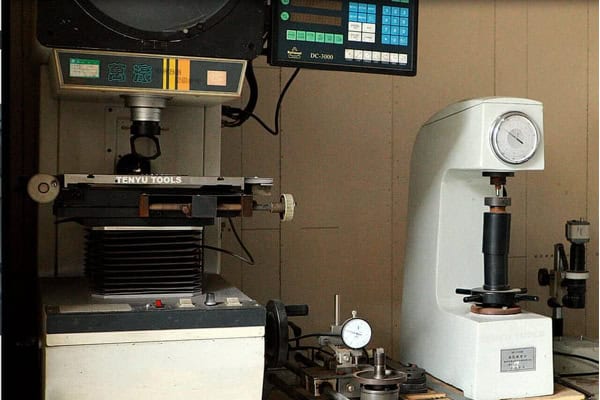
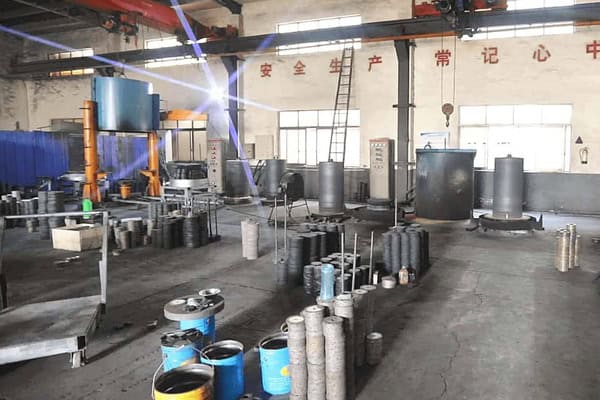
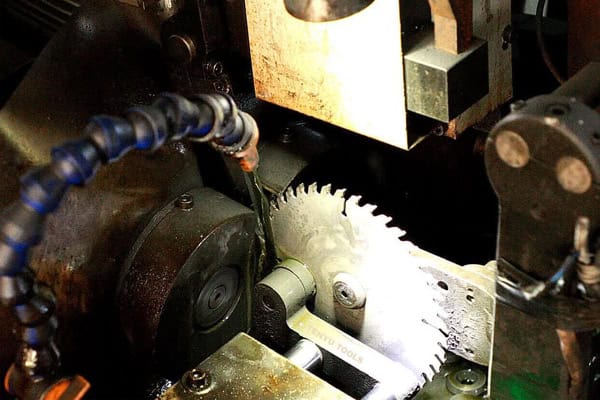
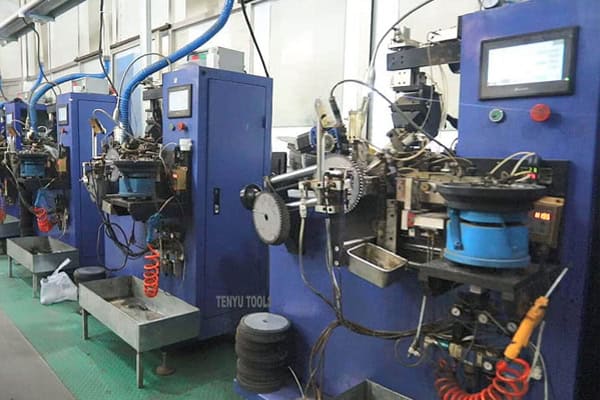
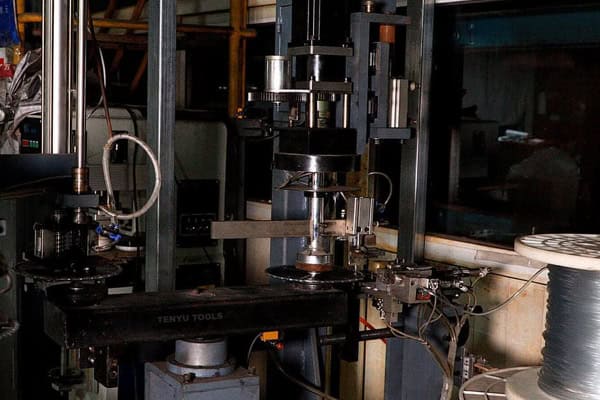
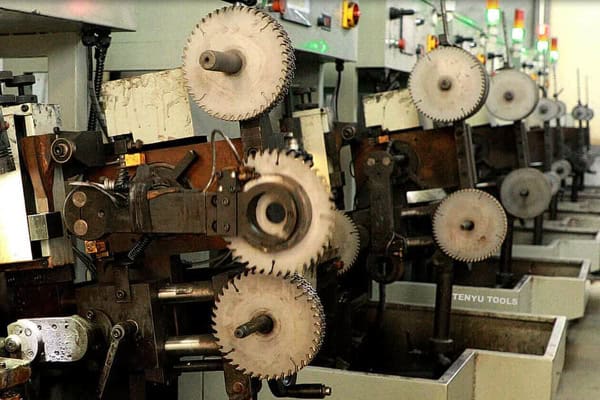

Get Free Quote
Contact us to get a free quote and more expertise about custom Saw Blade. Your project will meet a right solution with Tenyu Tool.
Custom Saw Blade With Easy
At Tenyu Tool, We turn complex Into Simple! Follow the following 3 steps to start today!

Tell us as specific as possible of your needs, provide the drawing, reference picture and share your idea.

We will work on the best solution according to your requirements and drawing, the specific quote will be provided within 12 hours.

We will start mass production after getting your approval and deposit, and we will handle the shipment.
Trusted By
Inspired by the Standards of Leading Saw Blade Brands, we are committed to continuously elevating our own brand and quality.
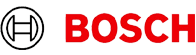
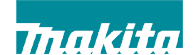
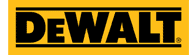
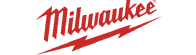
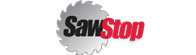
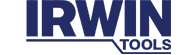